A Continuous Loop Chain Used to Suspend Product
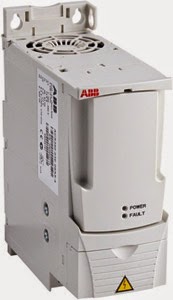
A continuous loop chain used to suspend product and move it from point to point or through a process.
Required Drive Features:
The drive can control multiple independent rates of acceleration and deceleration for the motor and load. These features control the amount of time the drive takes to increase or decrease the output during speed control.
Each application has specific requirements for I/O. Analog I/O is generally used to read process signals and output signals proportional to drive status. Analog I/O is generally Voltage (0-10V) or Current (0(4)-20mA). The type and number required by the application must match the drive.
Applications that involve multiple drives in a coordinated system often benefit from a common bus configuration. Drives are connected via their DC bus rather than the AC line. It allows energy to be shared between drives and reduces the number of components.
Specifies the amount of base speed that the speed reference is reduced when at full load torque. Use the droop function to cause the motor speed to decrease when an increase in load occurs. This function is normally associated with master/follower application.
Applications that require rapid deceleration or quick stops can regenerate energy back to the drive. A dynamic brake dissipates this energy through a resistor as heat.
High performance applications often demand nearly instant response to changes in speed or torque commands or input status changes. The higher the dynamic response, the more capable the drive is in meeting these demands.
Motors are rated by the manufacturer for the voltage resistance of the insulation system. If this insulation system voltage is too low, voltage reflection from the drive could cause motor failure. This is particularly important if the motor is a long distance from the drive and if the motor is an older motor being retained for the application.
Applications may require varying degrees of overload capacity for starting, accelerating, or intermittent duty. This overload capacity must be supplied by the drive as current and by the motor as torque.
An internal function provides closed loop process control with proportional, integral and derivative (PID) control. The PID function reads an analog input to the drive and compares it to a desired setpoint. The PID loop adjusts the drive output frequency (and therefore the process) to make the input value equal the setpoint.
A squirrel-cage motor slips under load. To compensate for this, the frequency can be increased as the motor torque increases.
All applications operate over a given speed range, defined as the ratio of maximum continuous speed to minimum continuous speed.
Applications that depend on accurate torque to accomplish the task require a drive that can control or 'regulate' torque. These applications typically control tension or force to produce a high quality product. The motor slip plus magnitude and phase angle of the output current are controlled to produce the commanded torque.
Recommended Choice: ABB ACS355 Series
Comments